Päivi Puntila, Business Development Director, Trimble’s BIM and Engineering Division, explores the integration of sustainability in construction with industry experts, AFRY. This article explores how embodied carbon calculations and material reuse in the demolition process contribute to reducing the carbon impact of new projects.
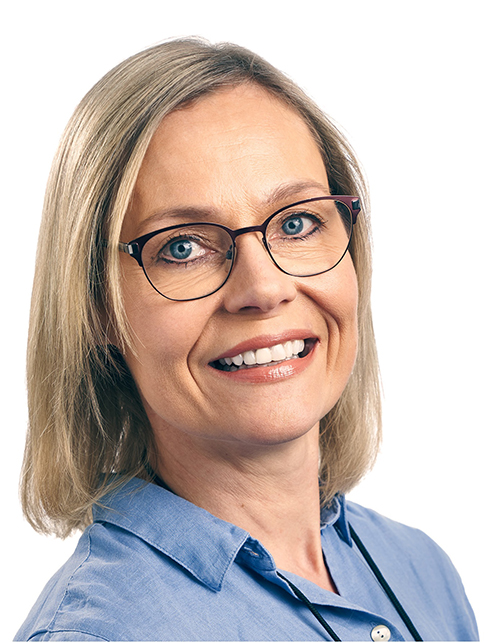
With sustainability concerns in focus, the global construction industry is increasingly including embodied-carbon calculations in environmental performance indicators. This means assessing the emissions impact at every stage of a project – from material extraction to end-of-life disposal.
The trend is accompanied by growing interest in the feasibility of reusing construction materials. When a building is demolished – or rather dismantled – incorporating the used steel, concrete and other building parts into a new construction project can help to minimise overall carbon impact. It also means fewer raw materials need to be extracted.
But just how practical is this? What changes would be needed at the industry level to scale such initiatives? How can structural engineers and BIM software contribute to the process? These are some of the questions that a team from global engineering consultancy AFRY set out to answer during a competition exploring material re-use.
The Finnish city of Espoo – one of the three cities that make up the Helsinki capital region – wanted to explore reuse ideas for a space called Keran Hallit. Constructed in the 1960s, the former logistics centre had been converted into a mixed-use space for startups, sports facilities and cafés in an area covering thousands of square metres. After serving in that capacity, the building is now slated for demolition, as the area is zoned for residential housing. The competition was aimed at bringing in ideas for sustainable and scalable re-use of the materials Keran Hallit is built from.
“We took on the project to try and establish some practices that could be more widely used,” says AFRY Finland’s Head of Sustainable Development, Arto Toorikka. “Solving global problems is at the core of our business. We think it’s really important to try and find new solutions for this issue.”
BIM objects in an open digital inventory
The team from AFRY designed a nine-stage circular process for re-using Keran Hallit’s steel beams, concrete and other materials. The City of Espoo selected the proposal as one of three winners that were then invited to submit a proof of concept.
AFRY’s process begins with a survey of the structures slated for demolition to assess possibilities for material re-use in a broad sense. In stage two the salvageable materials are identified, and in stage three the objects are modelled with Building Information Technology (BIM) into a digital inventory.
“You first have to classify the building parts that can be reused. We concentrated on beams, columns and slabs, using point-cloud scanning to make IFC objects out of these,” says AFRY Architect, Maiju Rinne-Kanto. “Trimble Connect Organizer was very helpful for making this digital inventory, as you can easily add the feature information to the IFC building parts. These IFC objects are crucial for the next step in our process.”
Step four is where AFRY’s transformative vision for material reuse really came to life. Here the building components – represented as IFC files – are housed in a SketchUp 3D Warehouse that industry participants can access. The idea is that before a new building is designed to replace a demolished one, the project owner can visit this digital marketplace to see what materials are available for reuse.
AFRY also identified around 30 features that are important when considering material reuse. These include freeze-thaw resistance, thermal insulation capacity, and information related to hazardous substances or microbes. This data is all available in the digital marketplace too.
“The idea is to compile this kind of digital inventory of a building some years before it’s scheduled for demolition. Then an architect would see all the parts that are available for re-use. Only then should the design of the new building be made,” says Toorikka.
“We essentially create a resource pool that goes in a loop. Project owners get ready parts – just like a box of Lego – without needing to transport in new material. It’s beneficial for the environment and hopefully in the future can be offered in a competitive way,” he says.
Changes needed at the industry level
One of the main barriers to realising AFRY’s vision is the absence of a standardised industry-wide BIM inventory. Cost considerations and compliance issues also pose challenges.
In Finland, for example, it can be challenging to obtain a building permit for re-use. The country maintains strict standards for safety and indoor air quality. Old buildings often raise concerns around hazardous substances used in original construction materials.
Circular efforts are not easy to introduce on a large scale, but through the Keran Hallit project AFRY has identified some key areas for development.
“We need a common platform that collects all the information on building parts that are available. Then architects and engineers can see what’s there before they start the work. You could even sell the materials through the platform,” says Rinne-Kanto.
“Re-use also demands closer collaboration between architects and structural engineers in the first phase of design,” she says. “An architect may think some materials would work well together, but the structural engineer may see something about their qualities that makes them unsuitable. Re-use is more complex in this way.”
While the practice of reusing building parts is still developing, it’s likely to become a more popular trend in coming years. Now is the time for the global construction industry to align its ways of working and collaborating in order to accelerate this transition to a more sustainable future.