Kevin Soohoo, Senior Director of the AEC Practice at Egnyte
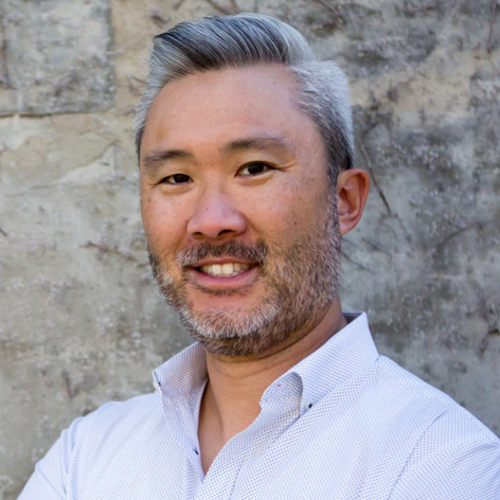
Digital Twins enable construction companies to model and analyse physical properties in perpetuity. The benefits of a Digital Twin are quickly transitioning from a nice to have to a necessity for companies doing work that demands efficiency, accuracy and compliance with evolving regulatory standards. Implementing Digital Twins in projects enhances project control by helping companies achieve sustainability goals, adhere to regulatory guidelines and more.
Integrating Digital Twins with the Building Information Modelling (BIM) process empowers firms to address key industry challenges such as reduced productivity, profitability and performance.
During construction, real-time monitoring systems can track progress, identify potential issues and analyse the performance of various systems for quick decision-making and problem resolution. Additionally, Digital Twins allow for the simulation of different construction scenarios and the analysis of potential outcomes. This predictive analytics capability helps anticipate issues, optimise construction processes and improve overall project efficiency.
Digital Twins foster better collaboration among stakeholders by providing a shared, up-to-date view of the project. This enhances communication and coordination across different teams and disciplines. Ensuring that files are the most current versions and reducing duplication makes it easier to locate information and avoid data sprawl. Effective version control and data management will become increasingly important as regulators mandate comprehensive safety regulations requiring extensive record retention.
Beyond the construction phase, Digital Twins provide valuable data for the maintenance and operation of buildings. This supports proactive maintenance, reduces downtime and extends the building’s lifespan. Digital Twins also benefit companies that must comply with safety regulations like the Building Safety Act by retaining accurate and detailed records of their projects long after completion. A realistic project rendering enables firms responsible for monitoring construction, maintenance, and ongoing safety compliance to perform these tasks efficiently and effectively.
Jeremy Suard, CEO and Co-founder at Exodigo
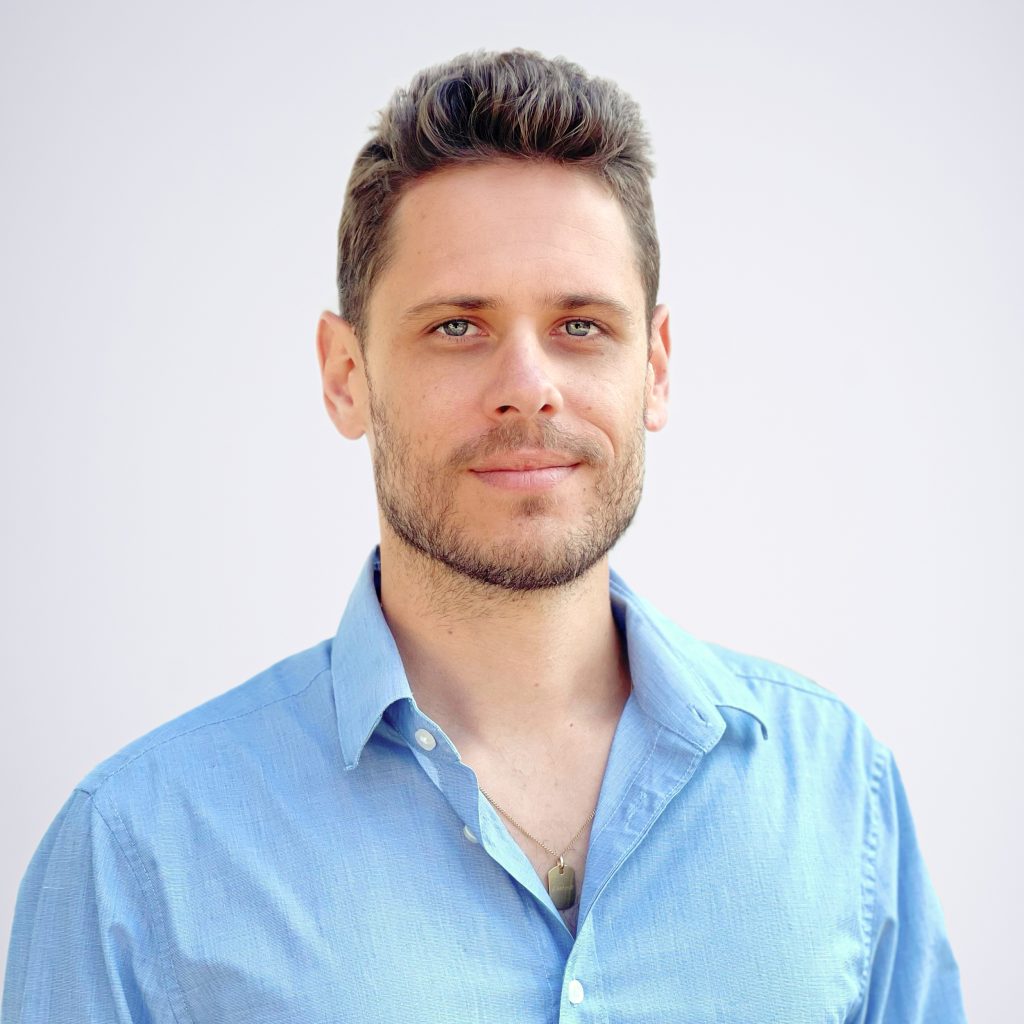
Digital Twins play a crucial role in construction safety and efficient use of project resources. A key element that is often overlooked in terms of ongoing monitoring and predictive maintenance is the need to understand what lies beneath the surface.
The unknown of the underground creates massive challenges for construction teams – from potentially dangerous utility strikes early in the build, to costly, unplanned rerouting work along the way or unstable foundations in the future. A powerful combination of advanced sensors, 3D imaging and AI technologies can now create detailed Digital Twins of the underground landscape that can scale to meet changing needs so project leaders can see the full picture, including what lies beneath the surface and properly plan ahead.
Underground Digital Twin technology is revolutionising the construction industry by providing a precise view of the underground – utility lines, bedrock and other potential challenges or changes. Armed with this critical data, construction managers can make informed decisions about what and where to build, while reducing risks, limiting redesigns and minimising delays due to uncharted obstacles.
A leader in underground Digital Twin technology, Exodigo’s multi-sensing underground mapping platform empowers construction managers to plan infrastructure projects that are delivered on time and within budget – fostering sustainable growth and development.
By building smarter, we can avoid problems instead of reacting to them. With a digital record, underground information is perpetually available to any organisation stakeholder. Digital Twins simplify the often challenging task of institutional knowledge transfer in our industry.
Michael Evans, Senior Director, Product Structures Division, Trimble
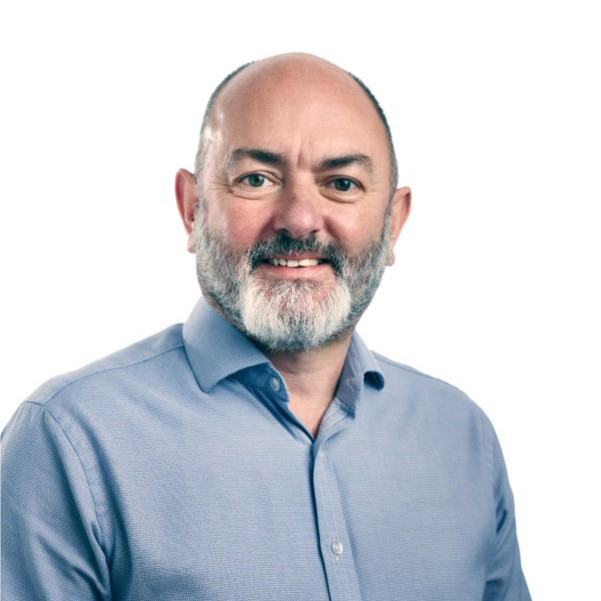
Digital Twins are the way to connect the physical and digital worlds. BIM models of assets comprise federated models from different trades: architecture, engineering, fabrication, construction, MEP and more can be further enriched with data from 3D scans and connected devices (IoT) and constructible, real-time data to turn as-built models into Digital Twins.
Elevating 3D models to Digital Twins increases analytical capabilities throughout all phases of a construction project. Digital Twins offer a better way — a visual common ground that offers invaluable cohesion through which construction phases can communicate more effectively. Component dimensions, model details, working conditions and more can be embedded into content-enabled models. Applying IoT devices delivering up-to-date information to their digital equivalent, the 3D model is then enabled to directly represent that physical asset on the spot. This helps monitor asset status.
All too often, important details get lost in translation as a model progresses down the chain of command. Digital Twin technology offers accurate, real-time updates of building progress that will reveal any deviations from 3D models. Trimble solutions make on-the-spot data collection and design verification faster and less resource-intensive.
Having the most up-to-date information on products or fabricated pieces of a structure (like the source of the material, the certification of the welds, etc.) embedded into content-enabled models allows for ‘Digital Twin builds’ — the quickest, most efficient and most accurate fabrication possible. Trimble can also collect this level of constructed/fabricated/manufactured data which would make the Digital Twin richer when Trimble products are used.
This approach reduces errors and rework, along with the time and money they waste. And, on-site scheduling is enhanced through real just-in-time production and delivery of fabricated components.
When the project is complete, Digital Twins can be handed over to the client to help support ongoing structural enhancements. For example, if a client is interested in the environmental impact of their structure, a Digital Twin can track energy demand, CO2 emissions and indoor air quality to help shape future green initiatives. A Digital Twin can be a value-added asset for clients looking to leverage data in future optimisation projects.
As for existing buildings or infrastructure, Digital Twins can be applied as a starting point for proactive maintenance. This starts with the creation of high-resolution 3D scans through by using mobile mapping systems or 3D (laser) scanners and applying AI-enabled technology to identify structural issues. The next step involves deploying the software to design sustainable mitigative measures based on construction technology that supports high-accuracy location-based construction. With that, the possibility unfolds to create a live Digital Twin that can serve as the basis for future maintenance, with facilities and maintenance data added to the twin on an ongoing basis, to support the asset during its entire lifecycle.
Digital Twins are, first and foremost, analytical tools that offer unprecedented insight into the condition of field investments and help inform future operations.
Hamid Alemohammad, Chief Operating Officer at Brickeye
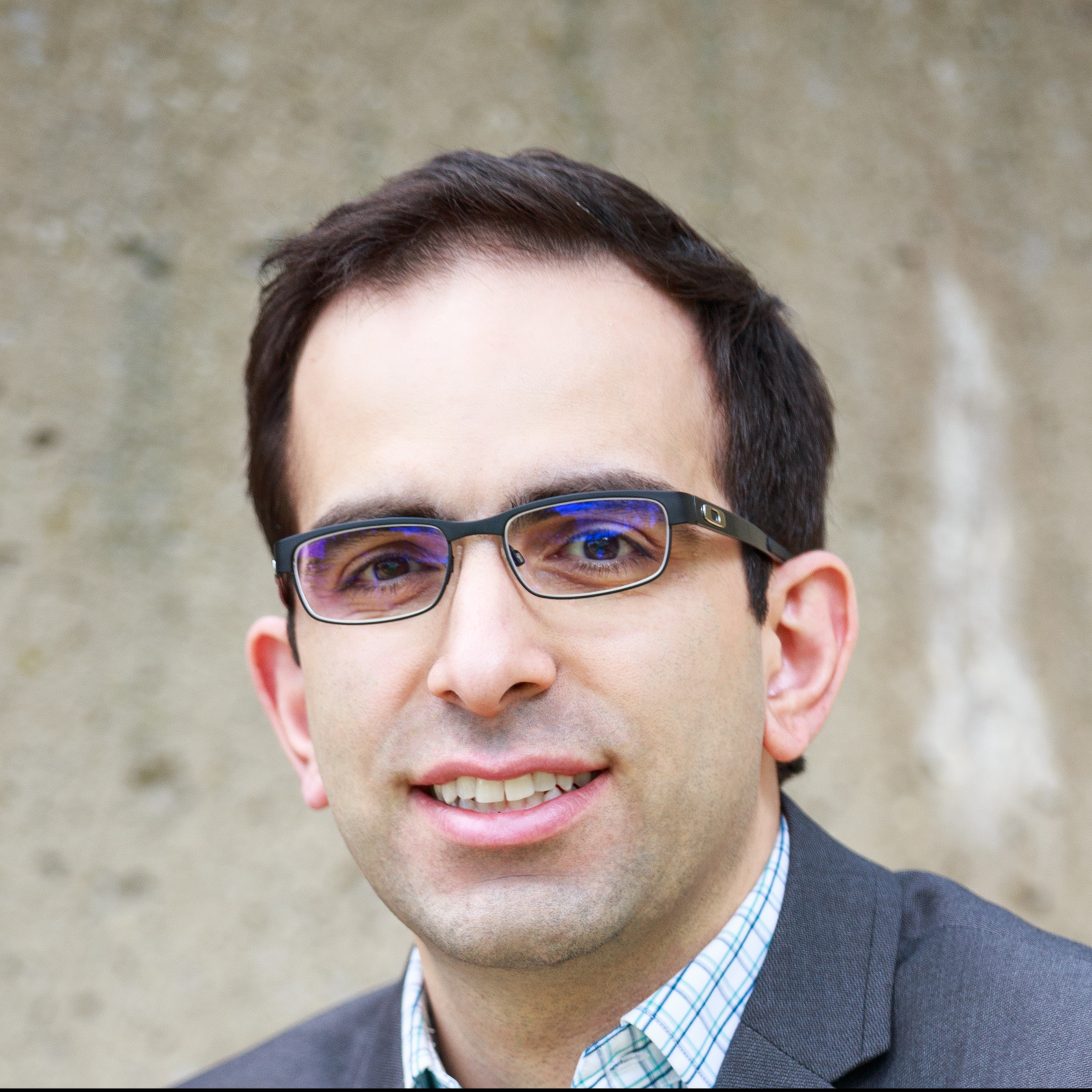
Real-time monitoring and predictive maintenance are critical considerations during the lifecycle of construction projects, from pre- to post-construction. The implementation of a Digital Twin can help construction stakeholders better understand and protect their project assets to make insightful and informed predictions on future performance trends, increasing efficiency, meeting compliance requirements and enhancing site productivity based on historical, current and predictive data.
As construction proceeds through the project lifecycle, different types of data are continuously captured – via on-site sensors and monitoring devices, combined with metadata obtained from other sources – allowing for a digital replica to be updated in real-time. Throughout construction, stakeholders can use this Digital Twin platform to gain a multi-dimensional view of the performance of the construction site – predicting trends, detecting risks, setting up automation for risk controls and optimising project schedules.
With the addition of real-time monitoring, Digital Twins mitigates construction risk through early detection of discrepancies – keeping project stakeholders updated on any potential abnormal conditions, incidents or tasks. Before the advent of digital technologies, frequent physical site observations and inspections were required to verify work done and determine the project status. With a Digital Twin platform and other on-site technologies, such as sensors and cameras, augmented data can verify the progress in real-time, without needing to step foot on the job site.
Other benefits include:
- Improved worker safety: Digital Twins enable companies to identify risk-associated areas to prevent unsafe activities and incidents in hazardous zones, and to ensure safe and effective usage of materials.
- Enhanced sustainability and efficiency: Real-time data is collected and analysed to generate insights into equipment utilisation, material tracking and energy consumption.
- Greener construction: Digital Twins can examine and predict the carbon footprint of different aspects of construction projects, offering insights on an ongoing basis about potential process improvements to reduce emissions.
Over the past several years, Digital Twin technology has made significant strides to modernise the construction industry and improve project construction with real-time monitoring and predictive analytics. Unlocking an advanced level of automation allows stakeholders to optimise processes, improve operational efficiency and mitigate risks. With comprehensive data and analytics, Digital Twins can aid in reducing waste, delays and reworks – while prioritising worker safety and sustainability in the wake of climate change – giving stakeholders the information and tools they need to make better-informed decisions to protect their projects.